Seven Key Factors To Help Maintain Arc Flash Safety
When an arc fault occurs, a massive electrical explosion can erupt. Here are the top arc flash measures that can limit the exposure of workers to the risk of arc flash and arc blast
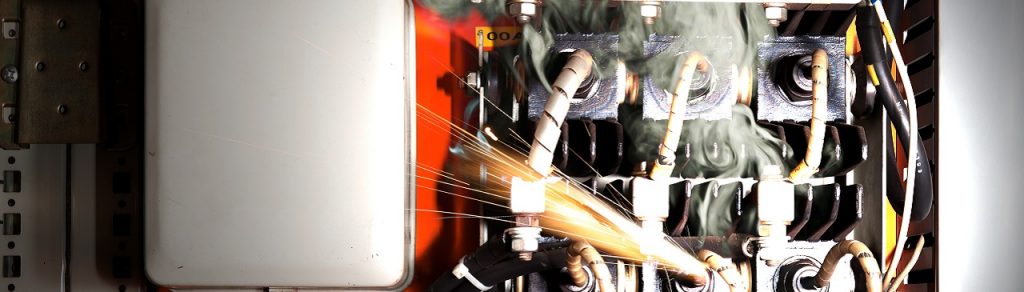
When an arc fault occurs, a massive electrical explosion can erupt. The light and heat emitted by this explosion is known as the arc flash, and the pressure wave is known as the arc blast. An arc flash releases hot gases and concentrated radiant energy up to four times the temperature of the sun’s surface, which can melt metal and cause severe burns, damage eyesight and result in fatalities. The accompanying pressure waves can damage hearing or brain function and send loose equipment, tools, machinery, and debris flying to cause further injuries. Even if an arc blast doesn’t injure a person, it will damage equipment and cause downtime.
One of the major causes of arc flash is voltage transients (spikes) resulting from switching reactive loads or lightning strikes. The transient may last only microseconds, but it may also carry thousands of amps of energy. When such spikes occur while measurements are being made, they can cause a plasma arc to form—inside the measurement tool, or in the air outside. Other major causes of arc flash are things as simple as touching a test probe to the wrong surface, worn connections, gaps in the insulation, improperly installed parts, or dust and corrosion that cause resistance heating.
The National Fire Protection Association (NFPA) 70E: Standards for Electrical Safety in the Workplace provides the most comprehensive guidance for protecting workers from electric shock and arc flash hazards. The 2015 Edition added several new provisions including strengthening electrical safety programs, new test instrument and PPE requirements, expanded training requirements, and redefinition of what constitutes a “Qualified Person” permitted to work in areas where there are exposed energized conductors and circuit components of greater than 50 volts.
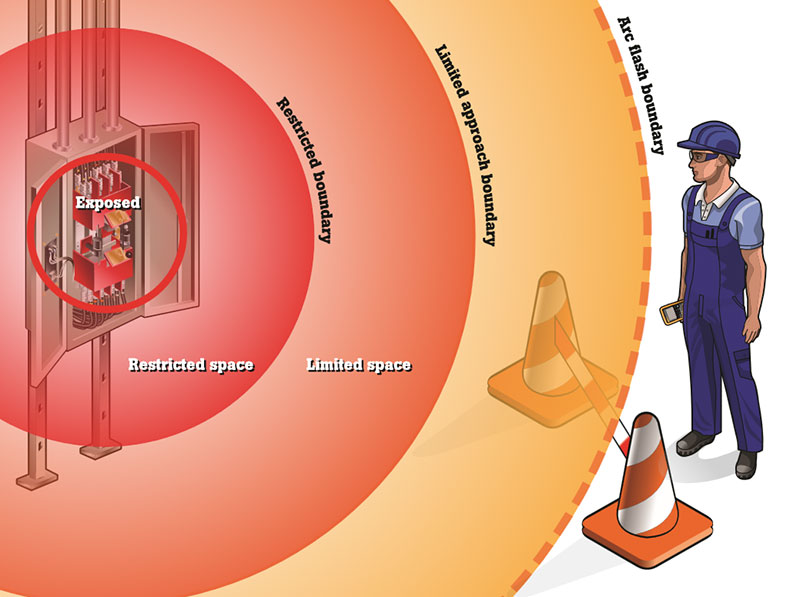
Here are top arc flash measures to limit the exposure of workers to the risk of arc flash and arc blast:
1) Train On Safe Work Practices
- Identify and avoid electrical hazards
- Follow safe work practices such as, proper lockout/tagout procedures, maintaining, hazard boundaries, and abiding by PPE requirements
- Understand emergency procedures.
- Qualified persons must have additional training on electrical equipment and power systems, to the point where they can demonstrate skills and knowledge of how the system is constructed, its manufacturer recommendations and associated hazards. Qualified persons must also receive training in:
- How to select the correct test instrument, how to inspect it, how to safely use it, what its limitations of use are and interpret the indications
- Skills and techniques to test for the presence and absence of voltage
- Skills and techniques to determine nominal (phase-to-phase) voltage of the electrical power system
- Safe approach distances for electrical shock and arc flash
- Perform safety job planning
- Assess the risk associated with a specific job task
- Select the appropriate methods from a hierarchy of controls, including PPE
- Safety-related work practices and procedures to allow them to perform the job task safely
- How to identify and understand the relationship between electrical hazards and injury
2) De-Energize Equipment Before Accessing
- Inspect your test tools and verify them with a known voltage source.
- Put on the appropriate PPE for the electrical environment.*
- De-energize and lockout/tagout the equipment.
- Test for absence of voltage
- Repeat the meter verification test.
*Until electrical circuits are tested and found absent of voltage, they must be considered energized.
3) Perform Regular Preventive Maintenance
Accidents happen… but some causes of arc flash can be prevented by regularly inspecting electrical distribution equipment.
During the inspection, pay specific attention to the early signs of physical failures that are known contributors to arc flash. Repeat the inspection on a regular basis, using a smart phone app such as Fluke Connect® or other portable means to both manage the list of critical components to inspect as well as keep previous/baseline readings field-accessible for the inspection team to compare against.
Knowing the health and history of the equipment in your facility is the first step to preventing arc flash. The key to being able to identify an abnormal reading is to gather baseline readings for especially important components and equipment. Critical components for arc flash safety include:
Electrical Connections — Use a thermal imager to scan energized components to quickly identify abnormally hot, loose connectors that can signal a variety of potential electrical failures from a safe distance. Make sure to follow all PPE requirements for the full arc flash assessment when opening and closing the door. Follow thermography-specific NFPA 70E PPE guidelines during the infrared inspection, including the distance to maintain from the panel as well as the personal safety gear to use.
Insulation — Test transformer windings, motor windings, and connecting cables with an insulation tester to check the integrity of the cable insulation or motor windings. Low insulation resistance readings may indicate that the cable is breaking down, potentially causing a short. This inspection can prevent premature equipment failure.
Circuit breakers — Proper testing of circuit breakers requires special equipment and specialized expertise. The breakers need to be removed from the circuit and tested to verify the trip current and delay.
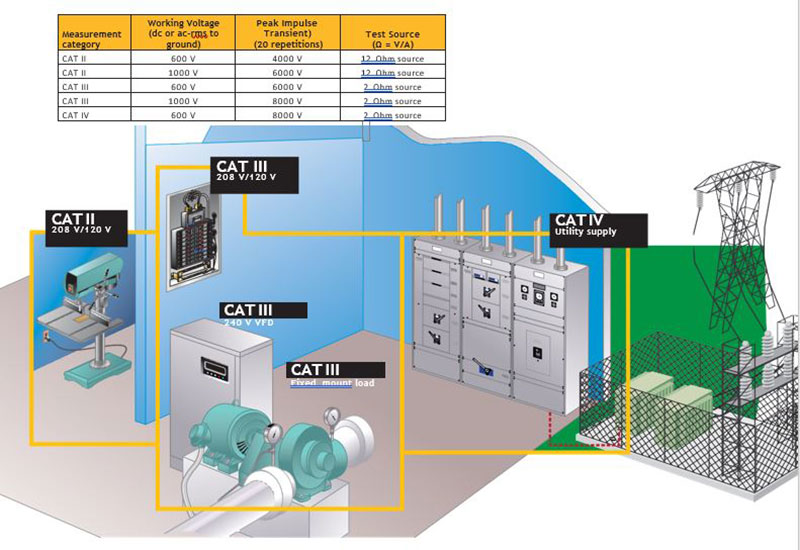
4) Wear Arc Rated PPE Within Arc Flash Danger Zone
Wearing the proper PPE in conjunction with the other safety measures is critical to minimizing injury in the event of an arc flash incident. In order for the PPE to perform effectively, its arc thermal performance rating must meet—or exceed—the thermal energy transfer during the arc flash incident. The best way to predict the thermal energy transfer, or incident energy, is through an arc flash hazard analysis. Then select PPE clothing and accessories based on performance rating predicted energy exposure NFPA 70E Table 130.7(C)(16).
5) Select Test Tools Rated For The Environment
Test tools, test probes, flexible clamps, and other accessories are considered part of PPE and must meet safety requirements established by such organizations as ANSI, the Canadian Standards Association (CSA), the European compliance standard (CE), and the International Electro-Technical Commission (IEC). Make sure your meter and accessories have the appropriate CAT and voltage rating for the electrical environment in which you will use them.
It is important to consider both the CAT and voltage ratings. For example, a CAT III 1000 V meter offers superior protection to a CAT III 600 V rated meter, but a CAT II 1000 V rated meter is not superior to a CAT III 600 V rated meter. That is because in calculating the voltage-withstand ratings, IEC 61010-1 test procedures take into account steady-state voltage, peak impulse transient voltage, and source impedance. The following chart shows those values in context of the top three CAT ratings.
Personal Protective Equipment Categories Always abide by the limits of use and minimum working distance. The following PPE categories are described by the National Fire Protection Association (NFPA) Standard 70E. The greater the electrical hazard, the higher the personal protective equipment arc rating must be to withstand an arc-flash incident. Always abide by the limits of use and minimum working distance. The following PPE categories are described by the National Fire Protection Association (NFPA) Standard 70E. The greater the electrical hazard, the higher the personal protective equipment arc rating must be to withstand an arc-flash incident.
6) Extend Your Safety Zone With Non-Contact Or Wireless Test Tools
Non-contact test tools allow you to take readings on an energized part without making contact. Wireless test tools enable you to attach the probes or clamp to the measurement target and remove yourself from the arc blast zone to read the results. Full PPE is still required whenever making contact with the energized system; however, non-contact tools may allow you to reduce the amount of PPE required while reading the measurement from a distance. Here are some of the most common non-contact and wireless tools for electrical inspections:
- Non-contact voltage detectors allow you to detect voltage during quick power checks without making contact with an energized part. Keep in mind that voltage detectors will only indicate power on the ungrounded side of the circuit; not on the grounded or neutral conductor side.
- Infrared thermometers measure temperature from up to several feet away. Just point the tool’s laser beam at the target and read the results on the display. This saves having to climb ladders, reach around hot, rotating equipment or reach into live panels. Infrared thermometers are available in a range of temperatures and accuracy levels.
- Visual infrared thermometers combine the convenience of a spot thermometer with the visual benefits of an infrared camera, providing accurate temperature readings at safe distances well beyond shock and arc flash boundaries. In addition to the standard IR thermometer features, visual thermometers provide an infrared heat map that blends with a standard digital image for quick identification of overheated conductors and terminations that could indicate pending equipment failures and possible arc flash issues.
- Infrared cameras capture thermal images of electrical components from beyond the arc flash boundary that can be used to readily distinguish temperature differences of components within the image (some degree of PPE is still required, see NFPA 70E). This helps operators quickly determine if corrective action is needed, and even how soon. According to the International Electrical Testing Association (NETA) a temperature difference between similar components under similar load between 4 °C and 15 °C indicates a problem with the higher temperature component, which should be repaired when possible. A temperature difference of greater than 15 °C, indicates the need for immediate repairs.
- Laser distance meters can be used to measure the lengths of conductor runs between equipment when conducting an arc flash study. This allows many distance measurements to be taken safely from the floor by just one person.
- Remote display multimeters allow technicians to attach the meter and probes (or clamp) at the measurement point and remove the display unit to a safe distance — or a better angle — to read the results. This allows you to close the door on a motor control center or stand at a safe distance as you measure motor inrush current.
- Wireless tools or sensors provide the most advanced technology for enhancing safety. Wireless-enabled test tools you can set up remote modules at the equipment and read the results on a smart phone or tablet and quickly identify and diagnose problems on energized equipment from a safe distance, well outside of electrical shock or arc flash boundaries. This can reduce the need for cumbersome PPE.
7) Install IR Windows In Panels
Installing properly certified infrared (IR) windows allows technicians to inspect electrical equipment without removing the panel cover. That makes it easier for companies to comply with NFPA 70E when inspecting switchgear and motors. In selecting IR windows look for:
- High visibility for thermal and visual inspections
- Certification for the highest arc blast test ratings — IEEE C37.20.7: 63 kA arc tested at KEMA
- Grounding to the metal enclosure to avoid the release of static electricity
- Easy to open covers that reduce the technician’s time within the hazard area
By installing IR windows that match these requirements you can significantly reduce work permit and NFPA 70E requirements for switchgear inspection.
Conclusion
Arc flash and arc blast are very real dangers in industrial electrical environments. By following best practices, using the proper equipment, and staying as far away from energized components as possible you can reduce your risk of those events and work smarter and safer.
Sean Silvey is a Product and Application Specialist for Fluke Corporation, focusing on electrical test and measurement tools, including multimeters, clamp meters, insulation, earth ground and installation testers. He has been with Fluke three years. Prior to that he worked more than 15 years in the commercial and residential HVAC/R industry.
source & content from:
https://www.manufacturing.net/safety/article/13195463/seven-key-factors-to-help-maintain-arc-flash-safety